Odor scrubber for drying ovens (food to feed)
Horizontal scrubber installation
The counter current scrubber consists of a horizontal, rectangular housing which is made of AISI 316L. In the event of counter current washing, the washing liquid, and the gas to be purified move in the opposite direction. The big advantage of counter current washing is that as the gas becomes cleaner, the concentration of the contamination in the washing liquid also decreases. In this way, the cleaning process throughout the installation remains particularly effective.
Get in touch with us
The scrubber is constructed, seen in flow direction, of three sections which are technically identical. Each wash section consists of hollow cone spray nozzles, part of which co-current and counter current. Each section is equipped with several spray arms that are mounted one after the other to obtain a long spray path and are constructed in such a way that the nozzles rinse the inside of the washing section well at the same time due to their joint large flow rate. The nozzles are mounted with an overlapping spray pattern, creating a very intensive cleaning system. This means that the contaminated gas cannot pass through the spray sections without being moistened and cleaned. As a result, a random packings is completely unnecessary, so that the pressure loss is very low and, above all, remains low.
Caustic soda (NaOH) section
Alkaline washing section with caustic soda solution for washing out the acid-forming components and any fat fumes. Spray section with a caustic soda solution for wetting and keeping the rectifier clean. Rectifier for laminating the gas flow. The rectifier is made up of removable cassettes, so that the rectifiers can be easily removed for inspection and possible cleaning. Droplet separator for removing the droplets from the gas stream and preventing contamination with the second washing section.
Sodium hypochlorite (NaOCl) section
Oxidative washing section with sodium hypochlorite solution to oxidize the odor-forming elements so that they can no longer cause odor nuisance. The dosage of sodium hypochlorite is controlled by means of a free chlorine sensor with integrated pH correction. The chemicals are dosed directly into the integrated buffer tank, where the free chlorine of the washing water is also measured so that the right amount of sodium hypochlorite is automatically dosed. Droplet separator for removing the droplets from the gas stream and preventing contamination with the second washing section.
Neutral section
Washing section with clean washing water for a final capture of water-soluble gas particles and any fumes from the sodium hypochlorite washing section. Double droplet separator as a final separator for removing the entrained droplets.
Dimensions | : | 6,200 x 2,500 x 3,000 mm |
Bedrijfs weight | : | approx. 10,000 kg |
Gas flow rate | : | 45,000 - 80,000 Am3/h |
Relativ humidity | : | 80 – 90 % RH |
Gas temperature | : | 58 – 65 °C |
Maximum dust load | : | 500 mg/Nm3 |
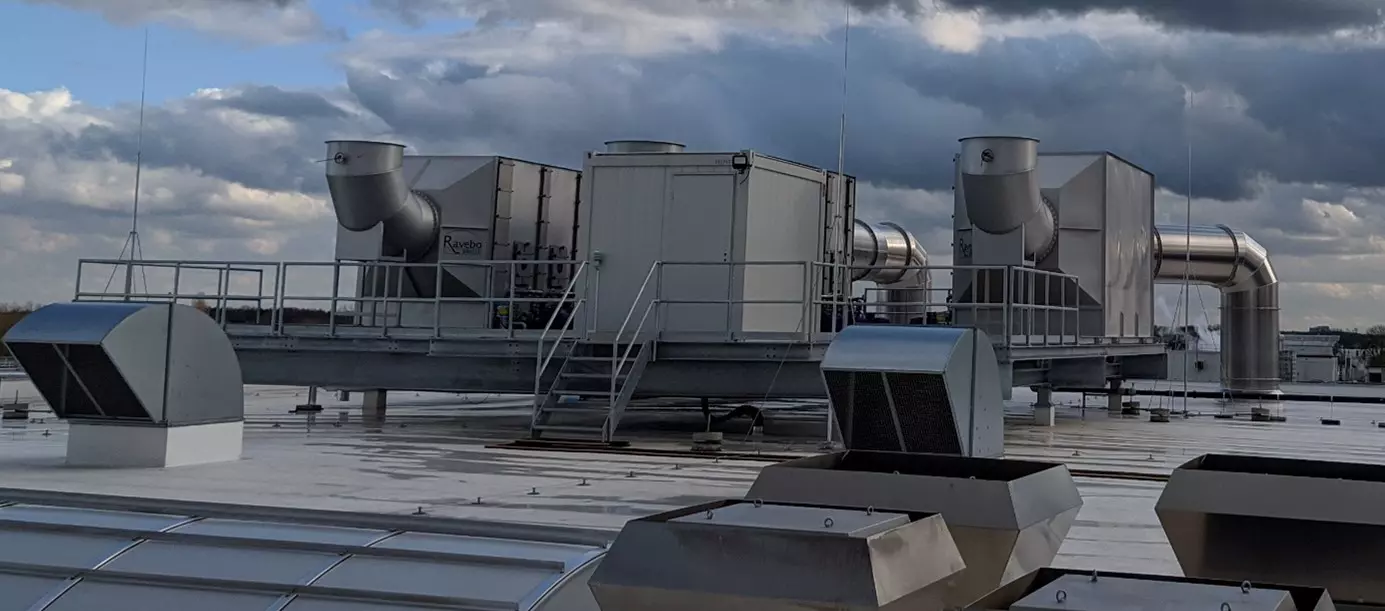
Package system
- Stainless steel 316 housing
- Siemens S7-1500 PLC in Rittal cabinet
- BRL accredated dosing system
- KSB centrifugal pumps
- Endress + Hauser instrumentation
- Centrifugal fan
- ECON valves
- Iwaki magnet drive dosing pumps